Shape memory alloys spring are embedded into a rotor-bearing system with low inherent damping in order to investigate the possibilities to use shape memory alloys to dampen rotor vibrations and to make the critical speeds of the system adjustable. Shape memory alloys exhibit damping properties due to hysteresis and their stiffness is dependent on their temperature. It is these properties that are used in the test-rig. The temperature is controlled by surrounding the shape memory alloy springs by heat chambers. The system also has a benchmark configuration with steel springs instead of shape memory alloy springs in order to compare the performance.
|
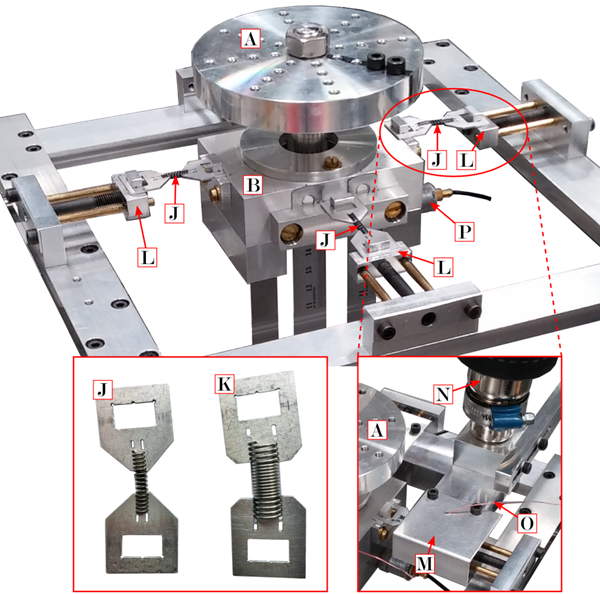 |
Test-rig. (a) fundamental part |
... and (b) spring attachment system |
(A) Disc on top of shaft; (B) upper and (C) lower passive magnetic bearings supported by (D) flexible beams; (E) SMA spring attachment point at the upper bearing; at the bottom of the shaft is attached a (F) flexible coupling and then a (G) DC motor. An (H) encoder measures the rotor rotation and (I) proximity sensors measure the rotor tilt angles. (J) SMA and (K) steel springs attached in (L) variable pretension mechanism. A (M) heat chamber can surround the springs fed with hot air from a (N) heat gun. The temperature is measured using (O) thermocouples. (P) Accelerometers measure the upper bearing motion. The global coordinate system XYZ is also highlighted. Upper part of test-rig highlighting the spring attachment system.
|